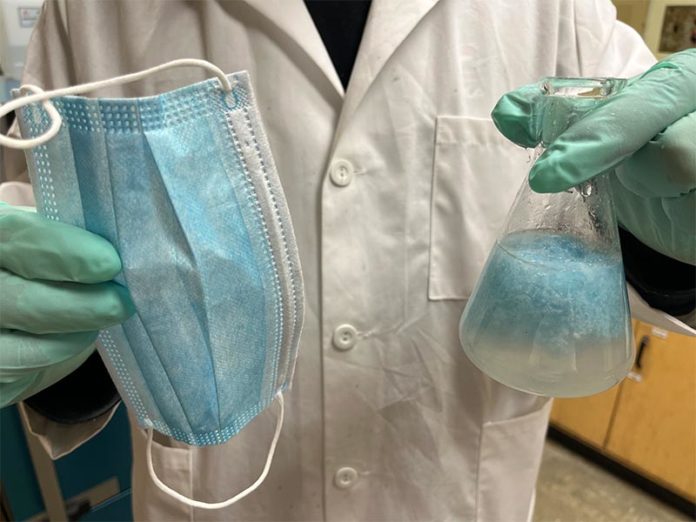
Dado que las mascarillas de un solo uso generalizadas durante la pandemia ahora presentan un problema ambiental, los investigadores han demostrado la idea de incorporar mascarillas usadas en una mezcla de cemento para conseguir concreto más fuerte y duradero.
En un artículo publicado en la revista Materials Letters, un equipo de investigación de la Universidad Estatal de Washington demostró que la mezcla que usaba materiales de mascarilla era un 47% más fuerte que el cemento de uso común después de un mes.
«Este trabajo muestra una tecnología para desviar las mascarillas usadas del flujo de desechos a una aplicación de alto valor«
“Estas mascarillas de desecho en realidad podrían ser un producto valioso si las procesas adecuadamente«, afirma Xianming Shi, profesor y presidente interino del Departamento de Ingeniería Civil y Ambiental y autor correspondiente del artículo. «Siempre busco flujos de desechos, y mi primera reacción es ‘¿cómo puedo convertir eso en algo utilizable en concreto o asfalto?‘»
La producción de cemento es un proceso intensivo en carbono, responsable de hasta el 8% de las emisiones de carbono en todo el mundo. A veces ya se agregan microfibras al concreto de cemento para fortalecerlo, pero son costosas. El hormigón reforzado con microfibras puede reducir potencialmente la cantidad de cemento necesaria para un proyecto o hacer que el hormigón dure más, ahorrando emisiones de carbono y costes.
Fibras útiles
Confeccionadas con un tejido de polipropileno o poliéster donde entra en contacto con la piel y una fibra ultrafina de polipropileno para las capas filtrantes, las mascarillas médicas tienen fibras que pueden ser útiles para la industria del hormigón. Si no se reutilizan, las mascarillas desechables pueden permanecer en el medio ambiente durante décadas y suponer un riesgo para el ecosistema.
«Este trabajo muestra una tecnología para desviar las mascarillas usadas del flujo de desechos a una aplicación de alto valor«, asegura Shi.
En su trabajo de prueba de concepto, los investigadores desarrollaron un proceso para fabricar diminutas fibras de mascarilla, de cinco a 30 milímetros de longitud, y luego las agregaron al cemento para fortalecerlo y evitar que se agriete. Para sus pruebas, quitaron los bucles de metal y algodón de las máscaras, los cortaron y los incorporaron al cemento Portland común, el tipo de cemento más habitual que se usa en todo el mundo y el ingrediente básico para el concreto, el mortero y la lechada.
Mezcla con óxido de grafeno
Mezclaron las microfibras de la mascarilla en una solución de óxido de grafeno antes de agregar la mezcla a la pasta de cemento. El óxido de grafeno proporciona capas ultrafinas que se adhieren fuertemente a las superficies de las fibras. Tales microfibras de mascarilla absorben o disipan la energía de fractura que contribuiría a las pequeñas grietas en el concreto. Sin las fibras, estas grietas microscópicas conducirían eventualmente a grietas más anchas y al fracaso del material.
Los investigadores están realizando más estudios para probar su idea de que las microfibras tratadas con óxido de grafeno también podrían mejorar la durabilidad del hormigón y protegerlo del daño por heladas y de los productos químicos descongelantes que se utilizan en las carreteras. También prevén aplicar esta tecnología al reciclaje de otros materiales poliméricos, como ropa desechada, para incentivar la recolección de dichos desechos.
Fuente: Materials Letters.